2025: 10 logistics KPIs to monitor to increase efficiency
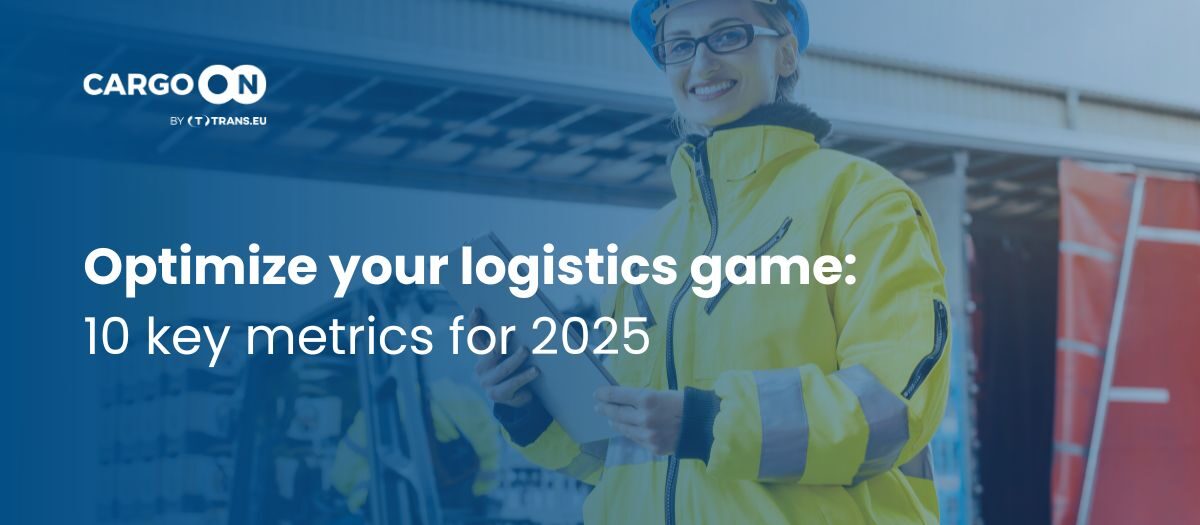
In the dynamic and competitive landscape of the European market in 2025, logistics managers face mounting pressure to adopt strategies that enhance efficiency and drive cost savings.
Monitoring the right key performance indicators (KPIs) is essential for optimizing processes and ensuring that operations meet customer expectations. But which KPIs are most relevant for manufacturing companies?
1. OTIF (On-Time In-Full)
What it is: The percentage of orders delivered on time and in full.
How to monitor: Track the number of orders meeting “On-Time” and “In-Full” criteria out of the total processed.
Why it’s important: Directly impacts customer satisfaction and operational capability.
How to improve: Implement real-time monitoring systems for order accuracy and delivery planning optimization.
2. On-Time Delivery (OTD)
What it is: The percentage of deliveries made on time.
How to monitor: Compare on-time deliveries to total shipments.
Why it’s important: Improves corporate reputation and customer loyalty.
How to improve: Leverage digital tools to optimize routing and monitor progress in real time.
3. Real-Time Visibility Monitoring
What it is: The percentage of shipments for which real-time location and status updates are accurately tracked and available.
How to monitor it: Compare the number of shipments with complete and accurate real-time tracking data to the total number of shipments.
Why it’s important: This KPI ensures that stakeholders have reliable and timely information to make informed decisions, reduce delays, and enhance customer satisfaction.
How to improve it: Implement Visibility Monitoring and Transport Order Execution solution to ensure seamless and accurate data collection and sharing.
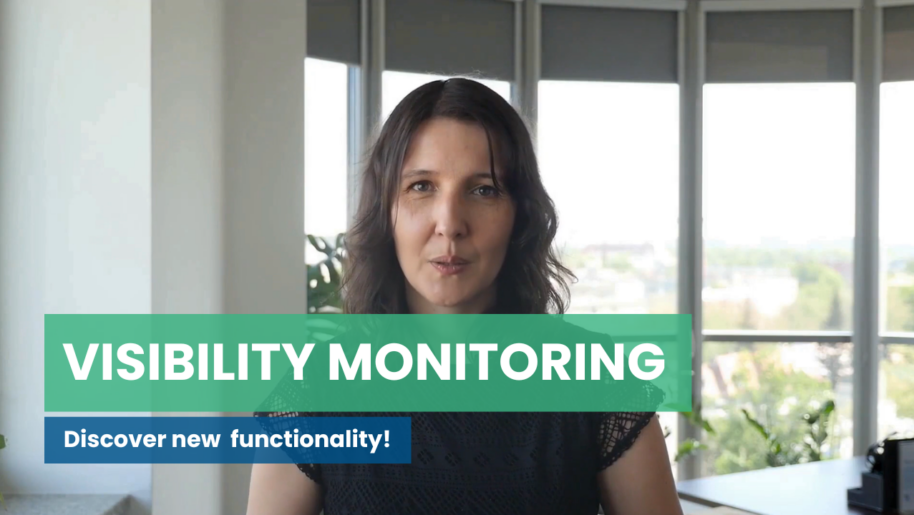
4. Load Utilization Rate
What it is: The percentage of transportation vehicle capacity used.
How to monitor: Divide the cargo weight or volume transported by the total vehicle capacity.
Why it’s important: Reduces operating costs and emissions.
How to improve: Use load planning software such as Goodloading to optimize available loading space and minimize empty runs.
5. Dock Waiting Times
What it is: The average time trucks wait for loading or unloading.
How to monitor: Record waiting times and calculate monthly averages.
Why it’s important: Reducing wait times accelerates operations and cuts demurrage costs.
How to improve: Implement time slot management systems to schedule arrivals and reduce downtime.
6. Order Accuracy
What it is: The percentage of error-free orders delivered.
How to monitor: Measure defect-free orders against the total shipped.
Why it’s important: Reduces returns, additional costs, and customer dissatisfaction.
How to improve: Digitize order management to minimize manual errors.
7. Cost per Kilometer Traveled
What it is: The average transportation cost per kilometer.
How to monitor: Divide total transportation costs by kilometers traveled.
Why it’s important: Identifies inefficiencies and helps lower costs.
How to improve: Optimize routes using routing software to minimize empty miles.
8. Backhauling Rate
What it is: The percentage of trucks completing return trips with payloads.
How to monitor: Compare the number of backhauls to total shipments.
Why it’s important: Reduces operational costs and environmental impact.
How to improve: Develop strategic partnerships to optimize backhauling opportunities.
9. Freight Order Acceptance Rate
What it is: The percentage of freight orders accepted by carriers out of the total freight orders sent.
How to monitor: Divide the number of accepted orders by carriers by the total freight orders issued.
Why it’s important: This KPI highlights the ability to meet transportation demand and identifies potential issues with carrier collaboration or capacity.
How to improve: Simplify and automate communication with carriers using a transportation order management platform. Ensure clear expectations and real-time updates to increase acceptance rates.
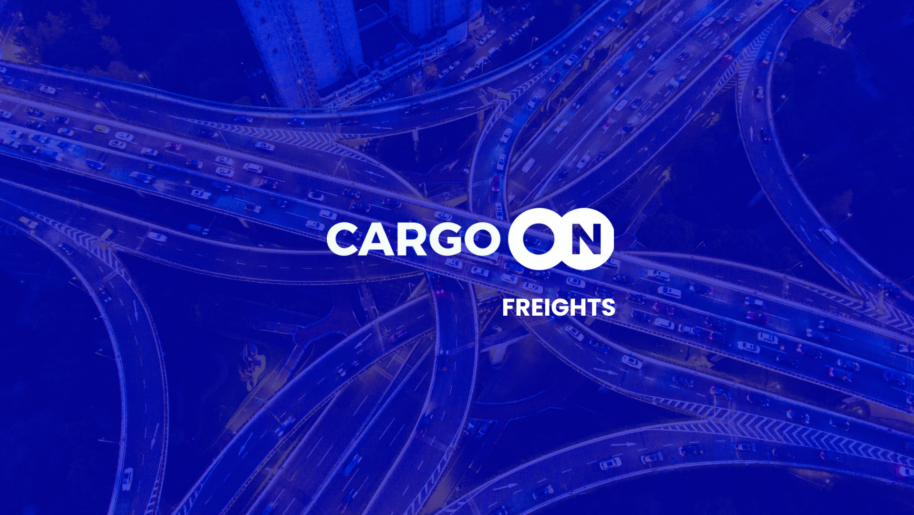
10. Carrier On-Time Rate
What it is: The percentage of shipments completed by carriers within the agreed timeline.
How to monitor: Compare the number of on-time shipments made by carriers to the total shipments.
Why it’s important: This KPI evaluates the reliability of logistics partners and helps identify recurring issues affecting service levels.
How to improve: Share real-time shipment data with carriers and use digital tools for tracking and communication. Analyze carrier performance by route and assign loads based on their strengths to enhance timeliness.
Solutions for tomorrow’s logistics
In a rapidly changing marketplace, monitoring KPIs and leveraging advanced digital tools are crucial for operational success. CargoON offers a suite of solutions to help companies digitize and optimize their logistics processes, improve efficiency, reduce costs, and enhance collaboration.
With analytical tools like Dashboard, businesses can gain a customized, real-time view of their performance, enabling them to identify inefficiencies and take proactive measures.