Unlocking Operational Potential: The Dock Scheduling Advantage
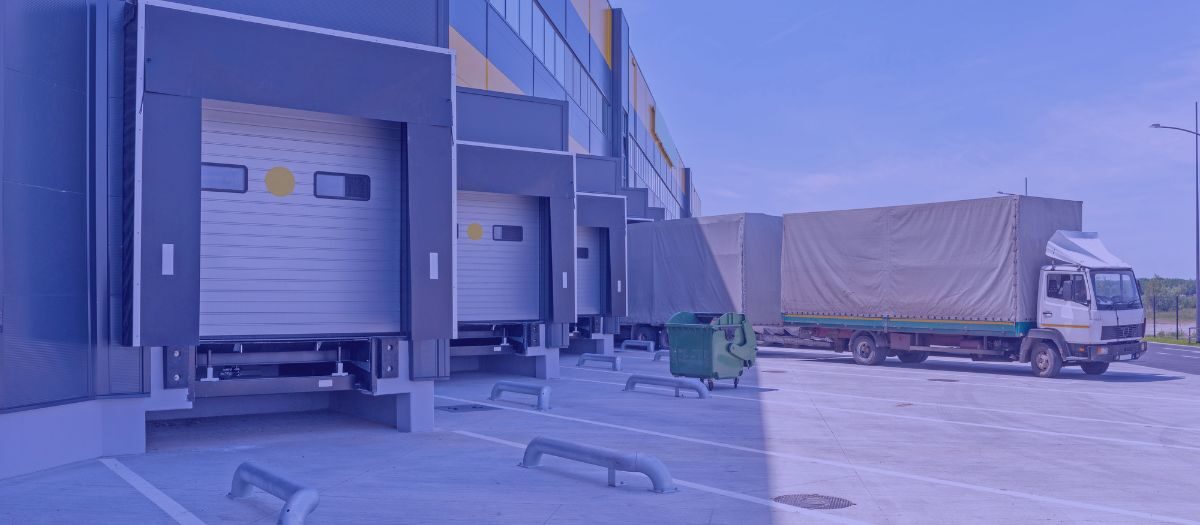
Last year, a study by the Spanish Logistics Centre (CEL) and CargoON found that more than 50% of carriers have to report warehouse arrival delays more than once per day. In recent weeks, a new study published by Federtrasporti has revealed that long loading times are still an issue in Italy too.
The figures in the Italian report, like the aforementioned CEL/CargoON study, as well as the September 2023 survey conducted by SCI Verkehr in Germany, all stress that the loading times issue is evidently something that needs to be tackled, in turn reinforcing the importance of digital solutions such as dock schedulers.
The scale of the problem
According to a study by Italian transport association Federtrasporti, in Italy, commercial goods vehicles remain stationary on average for four hours a day waiting to load or unload. This, says the report, is a significant problem not only for road haulage, but for the entire logistics chain.
The potential costs involved
The long waits generate additional costs for the haulage companies which are rarely compensated for. This could change in the foreseeable future, however. In its report, Federtrasporti referred to comments by Italy’s Minister of Transport that signal Italy could follow Spain in applying penalties to shippers that make carriers wait excessively long for loading or unloading. The inefficiency of the processes also inevitably lead to additional operating costs for both shippers and carriers.
The knock-on effects of loading and unloading delays
In an open letter sent out to various industry bodies on February 19, 2024, the Fai Conftrasporto transport association highlighted the severity of the problems associated with long loading and unloading times. The letter lists numerous problems, including a negative impact on drivers’ wellbeing, reduced safety at work, as well as increased transport costs. At the same time, the letter emphasised how efficient communication systems between clients and carriers can improve both logistics and safety. The letter also called on all trade associations to raise awareness among their members about the waiting times problem.
Uggè thus argues that this contributes to the shortage of drivers as it encourages people to choose alternative jobs that allow them to return home daily. Federtrasporti argues that the occupational health of drivers is also impacted through exacerbated problems with tiredness, stress, and muscle tension due to immobility. Moreover, it is said that drivers’ response times also take a dip after several hours of inactivity. This then compromises their ability to maintain concentration and drive vehicles safely.
The issues don’t end there either. Federtrasporti states that there are additional risks stemming from the accumulation of vehicles stopped at loading and unloading points. The association says the resulting congestion can increase the risk of accidents, including those involving dangerous or potentially contaminating substances.
What are Italian hauliers looking for?
To address this issue, Federtrasporti has made three recommendations. The first is to control and track parking times by collecting data from tools like tachographs. It says the process can identify anomalies and evaluate corrective solutions to be shared between the client and the carrier.
To reduce waiting times, Fai also suggests providing loading and unloading plans that are feasible and in line with the characteristics of the places where these activities take place. This means preparing appropriate communication and control systems that can communicate with the carrier and inform drivers in real time.
Finally, the letter called on shippers to comply with legislation that obliges carriers to compensate for delays at loading points that are outwith their control.
Figures from Germany
Meanwhile, figures from Germany show Italy is not alone in having this problem. A survey conducted in Q3 2023 by SCI Verkehr revealed that 72% of respondents faced recurring delays in loading at retail distribution centres. Although this percentage is still exceptionally high, it does mark a slight improvement from the equivalent figure in 2022 (86%).
The survey also indicated that wait times at loading ramps can be considerable. On average, drivers waited between 15 minutes and 2 hours, with 68% reporting waits of 1.5 to 2 hours.
According to German Industry portal DVZ, market analysts say the persistently long waiting times are often down to staffing shortages and organisational inefficiencies.
Using digital tools to address the issue
By utilising a dock scheduling system, loading docks can be effectively managed via designated time slots. This is purported to not only boost warehouse efficiency tangibly but also nurture stronger partnerships with carriers. Improved efficiency can additionally alleviate tensions among warehouse staff and minimise prolonged waits resulting from coordination issues.
Furthermore, a dock scheduler streamlines communication by centralising information, enhancing interactions among logistics departments, carriers, and warehouses, thus ensuring seamless operations as per a predetermined timetable. These tools not only evenly distribute workloads throughout the day, but also enable drivers to reserve and adjust arrival times based on transport statuses.
Certain dock scheduling systems also grant access to detailed reports containing key performance indicators, promoting a holistic understanding of all warehouse processes and facilitating ongoing enhancements.
Given the scale of the problems described above, those who have not turned to a digital solution yet appear to have a lot to gain by utilising one. Some major shippers who have made the switch can certainly vouch for this. Dawn Foods, for example, a well known American wholesale manufacturer and distributor of breads, baked goods, mixes, and other food products, has implemented dock scheduling to effect.
In a CargoON case study, Ronny Sauer, the company’s European Supply Chain Analyst, revealed earlier this year that Dawn Foods had cut down on the number of cases in which all trucks arrived at the same time:
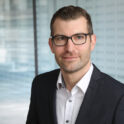
MFO. SA, a manufacturer of steel products, has also spoken of how the implementation of dock scheduling has made a difference.
“The solution makes it possible to optimise the management of the availability of workstations and ramps, the capacity of which can be defined in the system by the employee. In a short time, this allowed the company to generate real savings without increasing the number of shifts, staff and equipment. Thanks to the use of automation and data analysis, changes in the work of the warehouse were successfully implemented, resulting in the slot schedule,” said Ksenia Fiuk, Implementation Manager at MFO. SA.