Greci: optimizing food logistics through digitalization
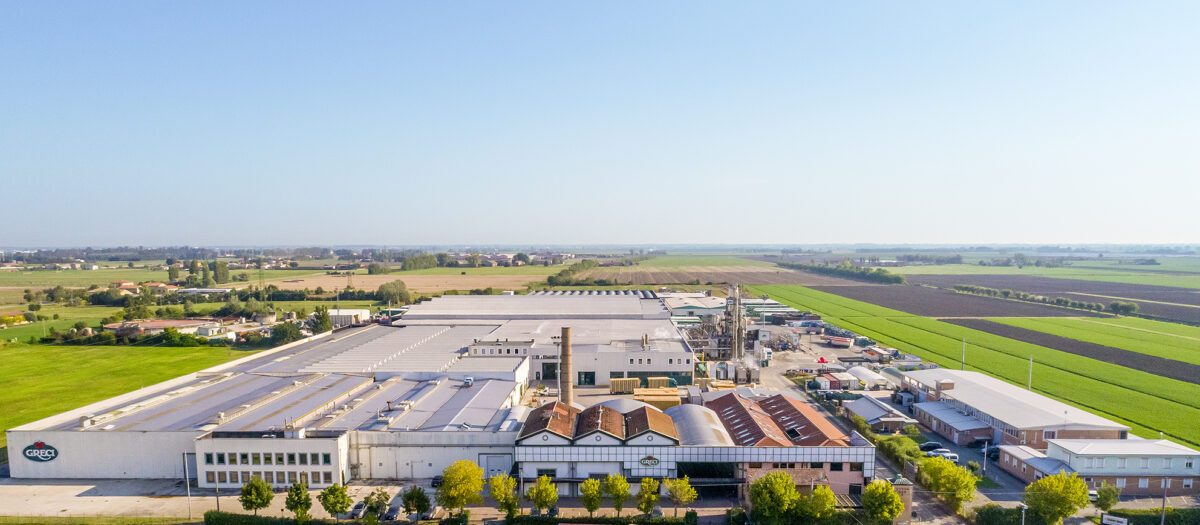
We had the pleasure of interviewing the Logistics Manager of Greci Industria Alimentare, a leading company in Italy’s Food Valley, to explore how the company has embraced innovation to overcome logistical challenges that could have hindered its growth.
Innovating for growth
- Greci Industria Alimentare
- With over 100 years of history, Greci is a cornerstone of the Italian food industry, known for producing high-quality ingredients for professional catering.
How to optimize logistics flow management through digitalization
Like all companies in the food industry, Greci faces logistical complexities that demand precision, efficiency, and flexibility. We discussed this with Fabio Rota, Logistics Manager at Greci Industria Alimentare.
What were the key logistical hurdles you had to overcome?
With around 200 employees, we process 140,000 tons of products annually and manage an average of 800 shipments per month across two warehouses. In recent years, the complexity of logistics and supply chain operations has increased significantly.
The main challenges were related to managing inbound and outbound flows. Coordinating supplier arrivals and transportation to customers has always been demanding, especially during seasonal peaks like the tomato season, when truck waiting times were particularly long.
When did you identify the tipping point for change?
For Greci, maintaining high-quality standards also means ensuring efficiency in logistics processes. When our traditional methods started creating bottlenecks that impacted productivity, it became clear that a change was necessary.
To optimize logistics flows, we set two concrete goals: reducing truck waiting times – both inbound and outbound – by 50% and cutting overtime costs by 20%. Additionally, we wanted to integrate a solution with our management system to digitize and automate key processes.
How did you approach choosing the most suitable solution?
We chose CargoON’s Dock Scheduler for three main reasons: its user-friendly interface, the scalability of the platform, and the speed of implementation.
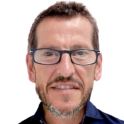
When it comes to digitalization, Italian companies are often said to resist change. Is Greci an exception to the rule?
Even though we fully understand the importance of innovation, resistance to change is always a factor. I believe that, in addition to the excellent work done by our IT department, CargoON’s active involvement was crucial to the project’s success.
Another common concern for companies is the uncertainty surrounding implementation timelines and the adoption of new tools. However, with CargoON, the integration process was quite straightforward. Within just a few weeks, Dock Scheduler was fully operational.
What tangible advantages have you experienced since integrating the new system?
The benefits became tangible in a short time. Within just a few weeks, we noticed a significant reduction in waiting times. Today, trucks no longer have to wait for hours, and loading and unloading operations are much faster and more efficient.
Additionally, with more effective planning, our operators have greater control over inbound and outbound flows, allowing them to work in a more organized and stress-free manner.
How would you advise other Italian businesses navigating similar obstacles?
Looking ahead, I believe that adopting Dock Scheduler has opened up new opportunities to further enhance our logistics processes. We can now tackle challenges with greater confidence and build a more collaborative and efficient digital supply chain alongside our partners.
Investing in digitalization is not just about adopting new technologies – it’s about transforming the way we work and making it better.